The company is committed to workplace safety and health, and strives to provide employees with a healthy and safe working environment. Therefore, any factor that may cause disasters, pollution, and occupational injuries is our target to eliminate.
Environmental Safety and Health Policy
The company was founded in 1977, engaged in the manufacturing, distribution, import, and export of personal hygiene products, primarily for all stages of life (baby, incontinence, and elderly care products).
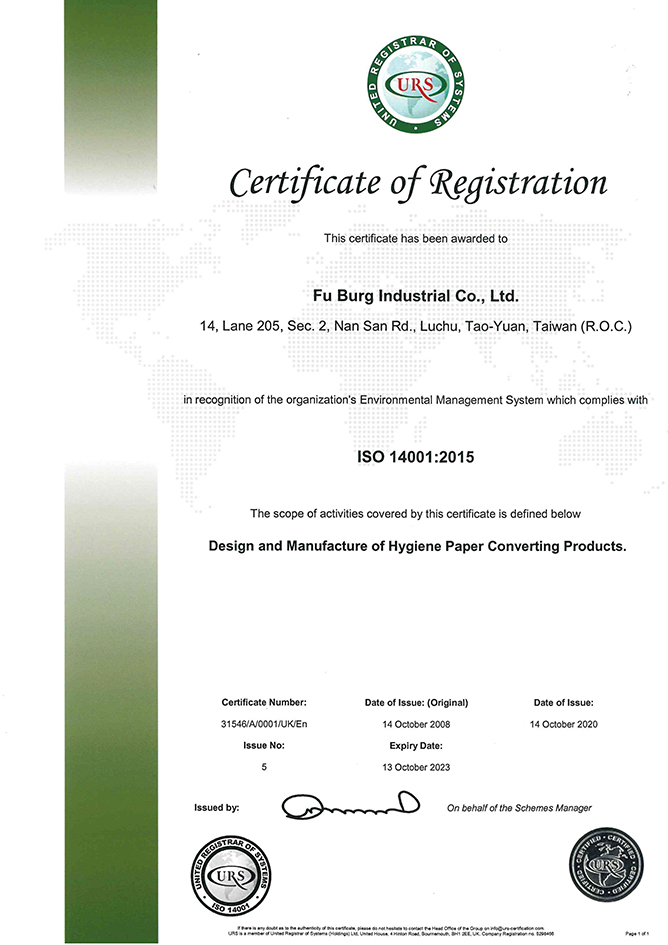
The company upholds the principles of “sustainable management and steady progress” while caring for employee health, maintaining a safe working environment, and prioritizing environmental protection. The company has implemented the ISO 14001 environmental management system in its factories, setting goals and targets, establishing an environmental management plan and implementation program to improve environmental performance, and ultimately obtaining long-term economic benefits. The company is committed to continuously improving its environmental, safety, and health management performance.
Environmental Protection
Fuburg conducts its business activities globally in a manner that contributes to the protection of the natural environment, complies with relevant laws and regulations, and strives to reduce waste. All departments are required to minimize their impact on the environment and protect the earth’s environment and ecology when engaging in business activities or designing and manufacturing products.
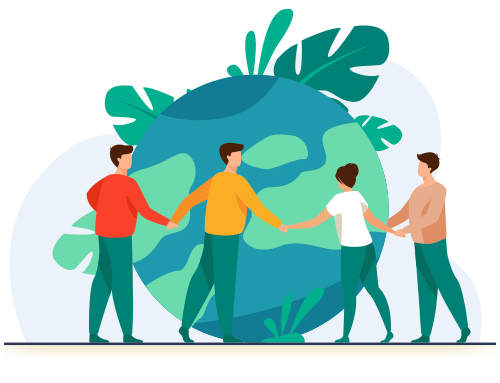
Environmental protection and occupational health and safety implementation instructions
The 5S Activity Promotion Office is responsible for occupational safety and environmental protection and is convened periodically by the plant department to review issues related to environmental protection, occupational hazard prevention, and health management.
Safety and Health Implementation Measures
- Regularly conduct fire safety and utility equipment inspections to ensure a safe working environment.
- Regularly hold fire safety lectures and practical safety and health education and training.
- Provide employees with regular health check-up services every year.
- All production staff are provided with earplugs, hairnets, and masks.
- All factory production machines are equipped with protective nets/covers, emergency stop lines, and emergency stop buttons.
- Hold occasional labor safety and health training, such as forklift safety operation and certification implementation.
- Conduct occasional emergency response plan drills.
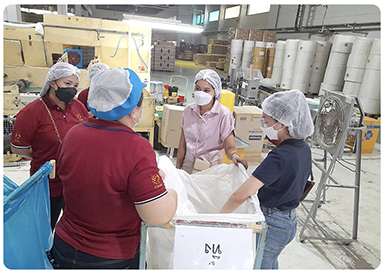
Work Injury Status: 2023
Item | Occupational accidents | Lost workdays (excluding holidays) | Number of occupational injuries | Total days absent | Absenteeism rate |
---|---|---|---|---|---|
Male | 0 | 0 | 0 | 0 | 0 |
Female | 0 | 0 | 0 | 0 | 0 |
Note 1: Work-related injury data is calculated based on the company’s monthly reporting of occupational accidents statistics.
Note 2: Absence rate = (Total number of days absent / Total scheduled work days) x 100%. Absences include personal leave, sick leave, menstrual leave, work-related injury leave, family care leave, maternity leave, etc.
Disability and Injury Frequency Rate: Fiscal Year 2023
Item | Number of Disabling Injuries | Disabling Injury Frequency Rate |
---|---|---|
Male | 0 | 0 |
Female | 0 | 0 |
Note: Disabling Injury Frequency Rate = (Total Number of Disabling Injuries x 10⁶) / Total Work Hours.)
Severity Rate of Disabling Injuries: Fiscal Year 2023
Item | Total Days of Disabling Injury | Severity Rate of Disabling Injuries |
---|---|---|
Male | 0 | 0 |
Female | 0 | 0 |
Note: Severity Rate of Disabling Injuries = (Total Days of Disabling Injury × 10⁶) / Total Work Hours
Measures for protecting work environment and employee safety
In order to provide a safe and healthy work environment for employees, the company continuously reminds and promotes ways to reduce the probability of occupational accidents. The protection measures for various operations are as follows:
1.Significant Environmental Considerations and Occupational Health and Safety Risk Control
Reference Number | Job Responsibilities | Category | Current Situation Explanation | Measures Taken / Implementation Status |
---|---|---|---|---|
1 | Environmental Consideration | Waste Management | The recycling equipment for cut materials often leads to environmental pollution due to improper handling during the collection process, resulting in scattered materials. | A solution has been implemented by redesigning and installing new recycling bins to prevent the scattering of recyclable waste caused by human error during operations. |
2 | Environmental Consideration | Waste Management | Reduced the average monthly waste transportation weight from 1.6 tons to 1.3 tons to improve waste management and decrease environmental impact. | Implement effective waste sorting and reduce the generation of household waste. |
3 | Safety and Health | Public Fire Safety | Due to frequent incidents of warehouse and factory fires within the jurisdiction of Taoyuan City, the excessive fire load has hindered firefighting teams from effectively entering for rescue operations, resulting in significant risks to nearby facilities. | The factory building is equipped with a smoke exhaust system, and in case of a fire alarm, the smoke exhaust equipment is automatically activated to ensure that in the event of a real fire situation, the elevated temperature caused by thick smoke will not hinder firefighting efforts. |
4 | Energy Conservation and Carbon Reduction. | Energy Consumption and Green Environmental Protection. | Energy Consumption of Air Compressors and Artificial Lighting | Implementation of Air Compressor Energy Saving Improvement Project and Factory Roof Natural Lighting Scheme |
2.Other Measures
- Regularly conduct environmental disinfection in employee work areas, restaurants, dormitories, elevators, stairs, etc., to maintain a healthy environment.
- Perform regular inspections on various public facilities such as fire protection systems, air conditioning, elevators, air compressors, forklifts, etc., to ensure a safe working environment and prevent harm to personnel.
- Conduct quarterly fire safety lectures and emergency response team drills to effectively reduce damage and risks in case of disasters or emergencies.
- Provide annual employee health check-up services to understand employees’ physical conditions and ensure their overall well-being.
- Outsource regular occupational environment assessments and drinking water testing in accordance with regulatory requirements to prevent harm caused by workplace factors and mitigate occupational hazards.
- Maintain a security presence by having security personnel patrol the company premises and dormitories regularly or on a random basis, both on regular days and holidays, to prevent accidents.